Best Automotive Welding Fixture Manufacturer And Factory In China
Company Development
- In 2011, TTM was founded in ShenZhen.
- In 2012, Moving to DongGuan; Building cooperation relationship with Magna International Inc.
- In 2013 Introducing more advanced equipments.
- In 2016, Introduced large-scale CMM equipment and 5 axis CNC equipment; Cooperated with OEM Ford Completed Porsche, Lamborghini and Tesla CF projects.
- In 2017, Moving to current plant location; CNC was increased from 8 to 17 sets. Top Talent Automotive Fixtures & Jigs Co.Ltd was established
- In 2018, Cooperated with LEVDEO automotive and completed the automotion production line. 4-axis high-speed CNC was introduced, the total Qty of CNC reached 21.
- In 2019, Dongguan Hong Xing Tool & Die Manufacturer Co.,Ltd was established. (One stop service) Cooperated with Tesla Shanghai and Sodecia Germany. Built a new R&D laboratory for automation.
- In 2020, Cooperated with OEM ISUZU in SA ;Completed the RG06 One-Stop Service.
- In 2021, Moving forward with the quality belief to create a world-class enterprise.
- In 2022, TTM Group office was founded in Dongguan City, New CNC 4 axis*5 sets, New Press*630 tons, Hexagon Absolute Arm.
- In 2023, TTM is building a new plant for checking fixture and welding fixture business; adding one 2000T press.
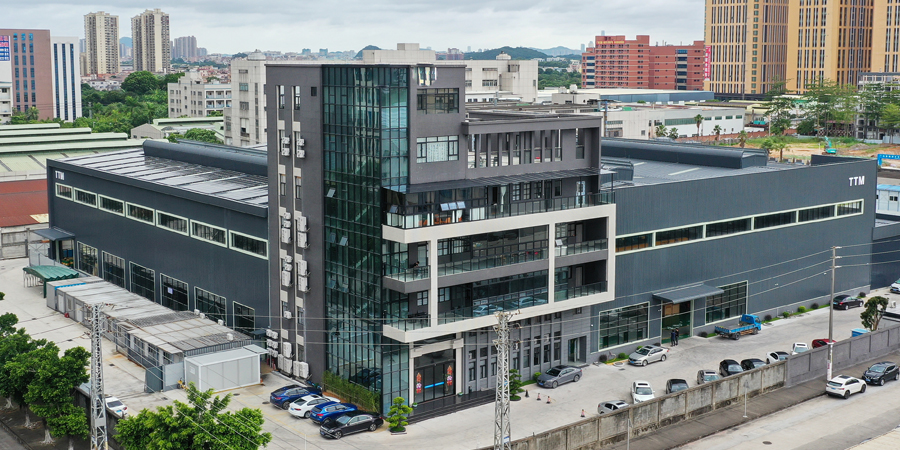
Checking Fixture & Welding Jigs Factory (Total area: 9000m² )
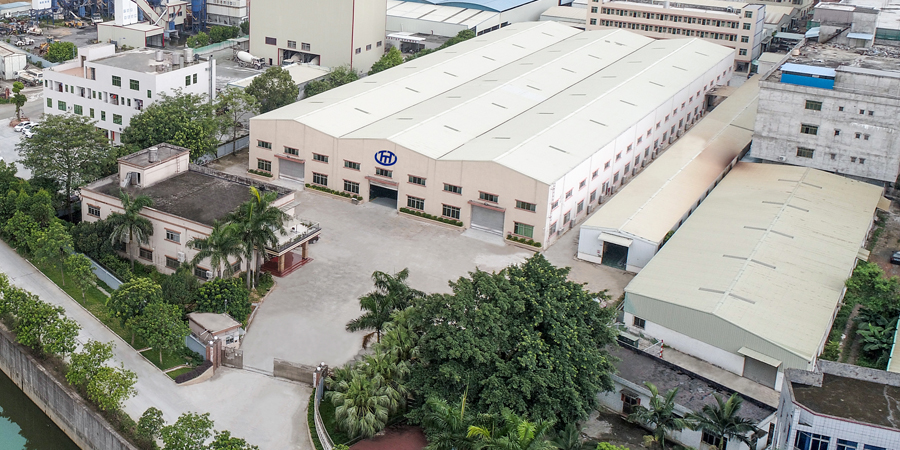
Stamping Tools & Dies and Machined Parts Factory (Total area: 16000m²)
Products Description
Product Name | Welding Fixture |
Application | Automotive CCB, Front End, WS Spring Link, Front Bumper etc. |
Welding Type | Spot Welding, Arc welding, (CNC/Assembly) Special welding fixture |
Pneumatic Component Brand | SMC, FESTO, TUENKERS, CKD, Manual clamp |
Electrical Component Brand | OMRON, Mitsubishi, Siemens, Balluff |
Material(Block, Locating Pin) | 45# Steel, Copper, Stainless Steel |
Operation Way | Robot Welding, Manual Welding, Special machine welding |
Controlling Way | Air Control(Pneumatic Control Valve), Electrical Control(Solenoid Valve ), Manual, No solenoid valve required Provide connector switch |
Clamping Way | Pneumatic, Manual |
Communication Way With Welding Cell | EtherCAT, PROFINET, CC-LINK |
Communication Relay Box | Electric box wiring way, Quick socket type, Solenoid valve island type |
Welding Fixture Base Type | Fixed on the floor, Positioner/Flip Tye |
Piping Way | Single layer tube, Flame retardant tube, Copper/Stainless Steel Tube |
Fixture Surface Treatment | Painting, Painting+Black Oxidization, Zinc-Coated, Powder Painting |
Lead Time | 2-4 Weeks for design and design review; 10-12 weeks for manufacturing after design approval 7-10 Working days for air shipping; 4-5 Weeks for ocean sipping |
Die Life | Depends on customer’s production capacity |
Quality Insurance | CMM Inspection Test with Samples Onsite Buy-Off Online video Web Conference Buy-Off Buy-Off Problems Solving |
Package | Wooden Boxes for samples;Wooden Boxes or Pallets for fixtures; |
Automotive welding fixtures are crucial tools in the manufacturing process of automobiles. These specialized fixtures are designed to ensure the precise alignment and assembly of various components, facilitating the welding of chassis, body panels, and other critical parts. In this comprehensive overview, we will explore the key aspects of automotive welding fixtures, including their importance, design considerations, fabrication, quality control, and their role in the automotive industry. 1. Importance of Automotive Welding Fixtures:
Automotive welding fixtures play a vital role in the production of automobiles for several reasons: Precision: They ensure the precise alignment of components, leading to consistent and accurate welds. This is critical for the structural integrity and safety of the vehicle.
Efficiency: Welding fixtures speed up the assembly process, reducing manufacturing time and labour costs. Quality Assurance: By holding parts in the correct positions, fixtures minimize the risk of errors and defects in the final product. Consistency: Fixtures deliver consistent results, regardless of the operator's skill level, which is essential for achieving uniform vehicle quality. 2. Design Considerations: Designing automotive welding fixtures is a complex process that involves careful consideration of various factors: Vehicle Model: The fixture's design must correspond to the specific make and model of the vehicle being produced. This requires a deep understanding of the vehicle's assembly requirements. Part Positioning: The fixture must accurately position various vehicle components, such as body panels, chassis sections, and frame components. This involves precise location points, clamping mechanisms, and support structures. Tolerance and Alignment: Engineers must consider tight tolerances and alignment requirements to ensure that the components fit together perfectly.
Material Selection: The choice of materials for the fixture is crucial. It should be durable, heat-resistant, and rigid to withstand the welding process. Ergonomics: Fixtures should be designed for ease of use and operator safety. This includes considerations for access, visibility, and ergonomics during welding operations. 3. Fixture Fabrication:
The fabrication of automotive welding fixtures involves several stages:
CAD Design: Designers create detailed 3D CAD models of the fixture, specifying the position, orientation, and clamping points for each component. Material Selection: Based on the design specifications, the appropriate materials, often steel or aluminium, are chosen for the fixture's construction. Component Manufacturing: Individual components, including support structures, clamps, and positioning elements, are manufactured precisely using CNC machining and other specialized techniques. Welding and Assembly: Skilled welders and technicians assemble the components, ensuring that they fit together accurately and securely. Testing: The fixture undergoes rigorous testing to ensure it meets the alignment and tolerances required for accurate welding. This includes test fitting of vehicle components. Calibration: The fixture is calibrated to ensure that it remains in perfect alignment and retains its structural integrity. 4. Quality Control: Maintaining high-quality standards throughout the fixture's fabrication process is essential: Inspections: Regular inspections are conducted to verify the accuracy, durability, and functionality of the fixture components.
Tolerance Checks: Precise measurements and tolerance checks are carried out to confirm that the fixture meets the required standards.
Alignment Verification: Fixtures are verified to ensure they maintain the correct alignment and orientation for assembly. 5. Role in the Automotive Industry: Automotive welding fixtures are integral to the automotive manufacturing process: Chassis Welding: Fixtures ensure the accurate alignment of chassis components, including frame sections and suspension components. Body Panel Welding: They hold body panels, such as doors, hoods, and fenders, in the correct positions for welding, contributing to the vehicle's overall structural integrity. Seam Welding: Fixtures are used in the welding of seams, joints, and connections to create strong and reliable bonds.
Welding Automation: In many cases, welding fixtures are integrated with robotic welding cells for automated production, further improving efficiency and consistency. 6. Customization for Automotive Manufacturers: Automotive welding fixture manufacturers often specialize in creating custom fixtures tailored to the unique needs of individual automotive manufacturers. These fixtures are designed to meet industry-specific standards and requirements, and they can be adapted for different vehicle models within a manufacturer's product line. In conclusion, automotive welding fixtures are a critical component of the automobile manufacturing process.
Solutions(Turnkey Solutions Service)
Body In White Assembly Systems:
1, Complete Car Body Welding Line
2, Single Stand-alone Welding Cell
CCB ASSY Welding Fixture, Floor Pan ASSY Welding Fixture, Wheelhouse ASSY Welding Fixture, AB Ring ASSY AB Welding Fixture, Seat ASSY Welding Fixture, Front Seat Cross Member Welding Fixture, Front End ASSY Welding Fixture, Dash Panel ASSY Welding Fixture, Cowl ASSY Welding Fixture and Rocker ASSY Welding Fixture manufacturer, design company and factory.
ISO Management System For Welding Fixture
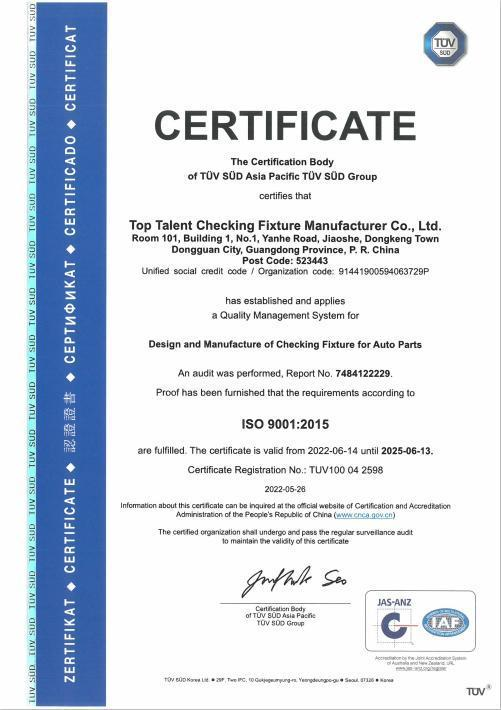
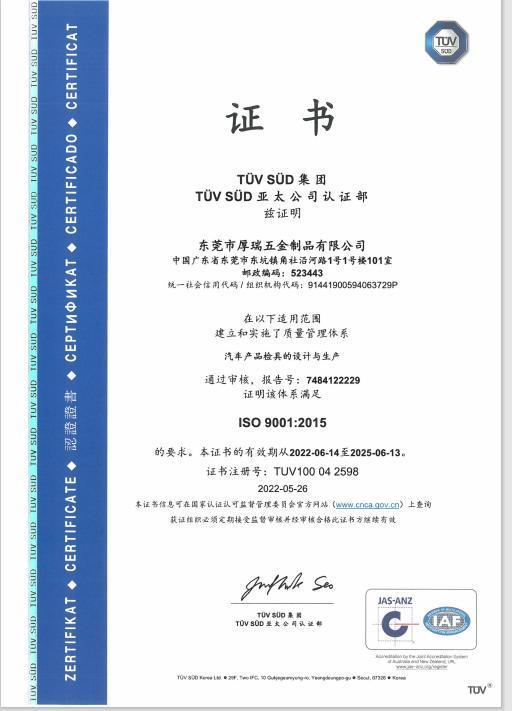
Our Welding Fixture Team
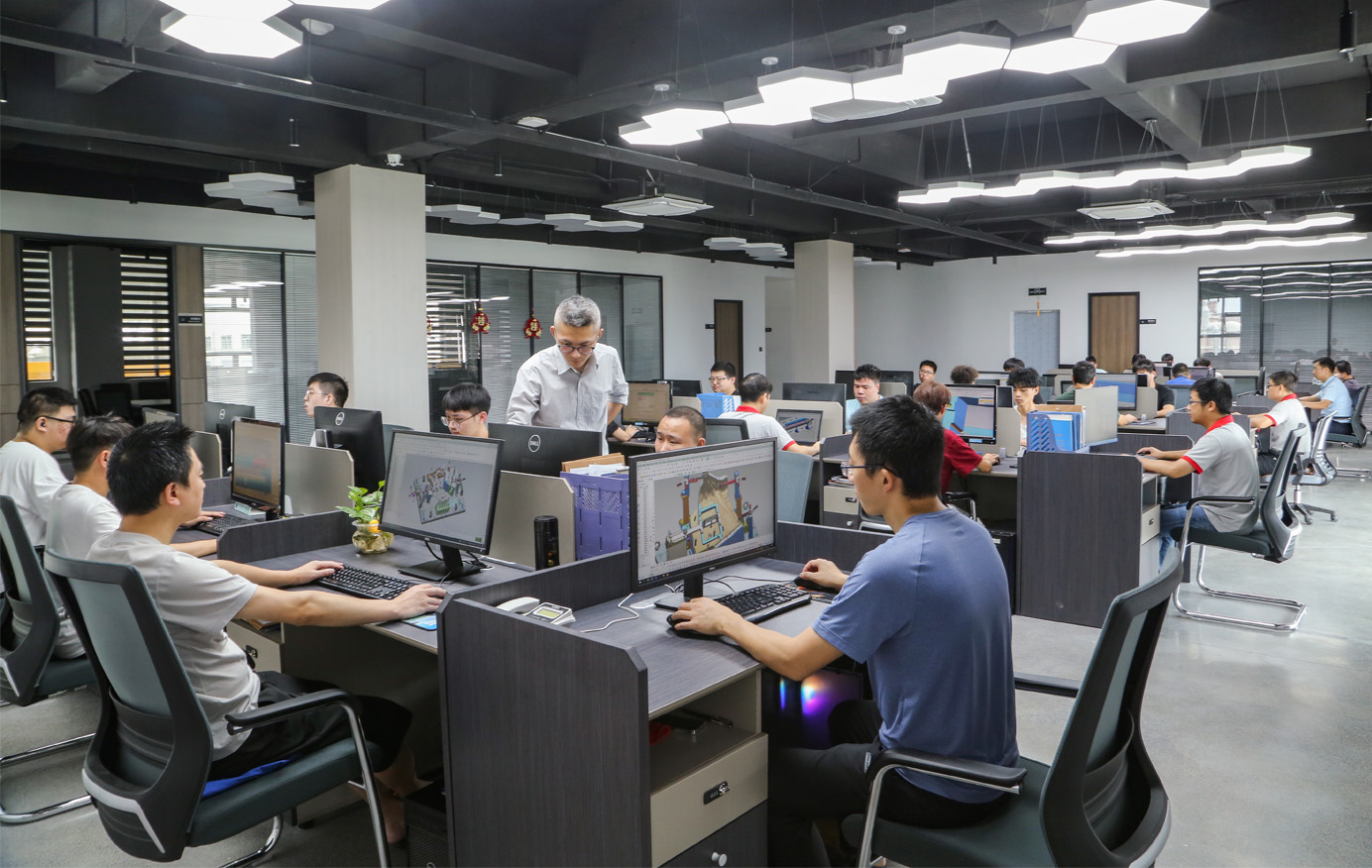
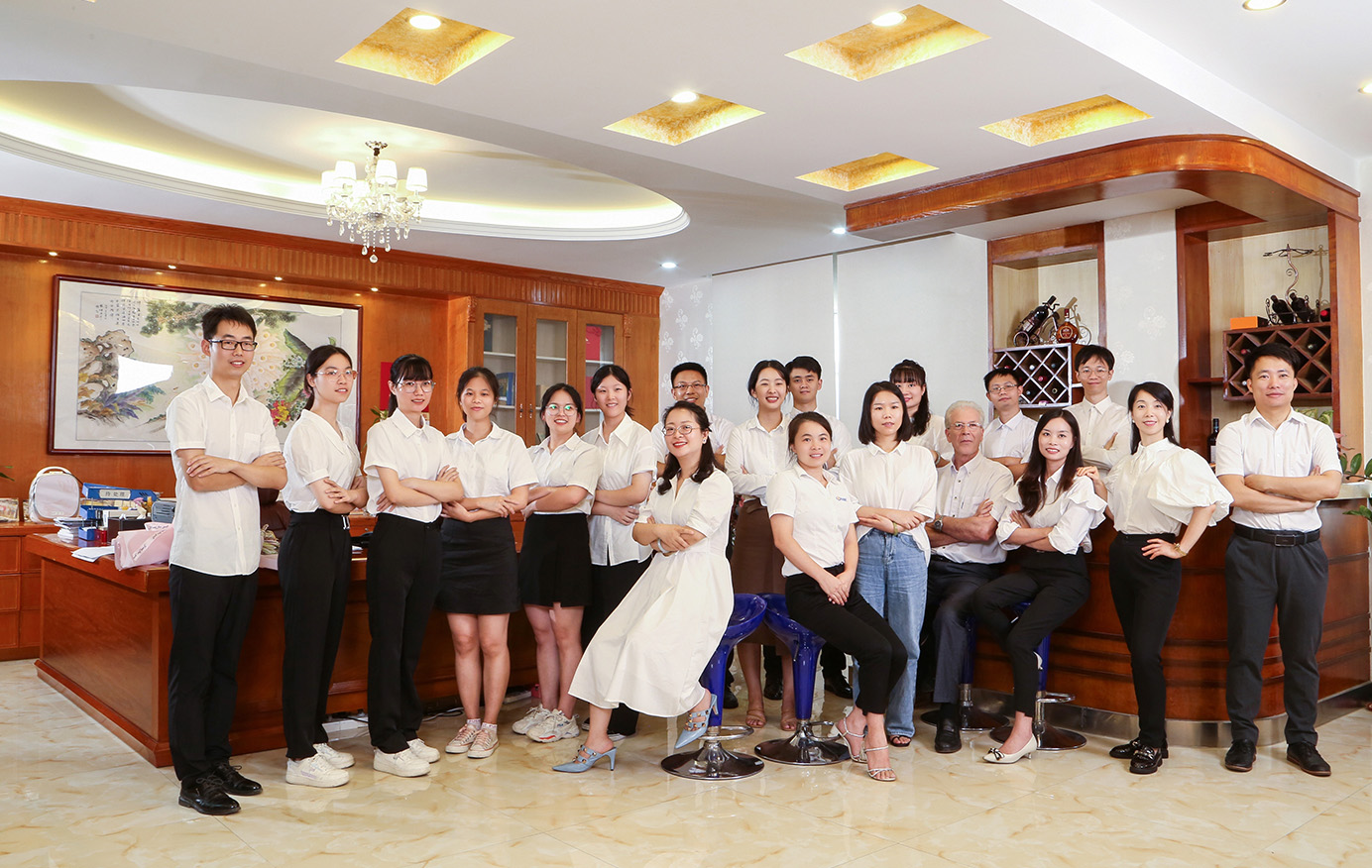
Our Advantages
1.Rich experience in automatic manufacturing and enterprise management.
2.One Stop Service for stamping tool, checking fixture, welding fixtures and cells to achieve timing and cost saving, communication convenience, to maximize customer profits.
3.Professional engineering team to finalize the GD&T between single part and assembly component.
4.Turnkey Solution Service-Stamping Tool, Checking Fixture, Welding Fixtures and Cells with one team.
5.Strong capability with international technical support and partnership cooperation.
6.Big capacity: Checking Fixture, 1500 sets/year;Welding Fixture and Cells, 400-600 sets/year; Stamping Tools, 200-300 sets/year.
We have more than 352 employees, 80% of which are senior technical engineers. Tooling division: 130 employees, Welding fixture division:60 employees, Checking fixture division:162 employees, We have a professional sales & project management team, long-term service overseas projects, from RFQ to production, shipment, after-sales, our team can handle all problems for our customers in Chinese, English and German Language.
Major Projects Experience Of Welding Cells And Welding Fixtures
Major Welding Fixtures Project(2019-2021) | |||||
Item | Description | Type | Project Name | Qty(Sets) | Year |
1 | CCB WF | Arc Welding | VW MEB31 | 60 | 2019-2021 |
2 | CCB WF | Arc Welding | VW MEB41 | 10 | 2020 |
3 | CCB WF | Arc Welding | VW 316 | 4 | 2020 |
4 | CCB WF | Arc Welding | Ford T6 | 8 | 2021 |
5 | CCB WF | Arc Welding | ISUZU RG06 | 3 | 2020 |
6 | CCB WF | Arc Welding | Bcar,BSUV | 6 | 2020 |
7 | CCB WF | Arc Welding | Bcar,BCAR | 7 | 2020 |
8 | Floor Pan WF | Sopt Welding | SK326/0RU_K Karoq RU | 15 | 2019 |
VW316/5RU_K Tarek RU (19003) | |||||
9 | WS Spring Link WF | Arc Welding | WL/WS | 4 | 2019 |
10 | Crossmember Brackets WF | Arc Welding | WL/WS | 12 | 2019-2021 |
11 | Front Bumper WF | Arc Welding | VW281 | 14 | 2019 |
12 | Chassis WF | Arc Welding | ISUSU RG06 | 18 | 2019 |
13 | SL ASY and MBR and EXT ASY | Spot and Arc Welding | Ford P703 | 25 | 2019-2021 |
14 | CCB WF and Wroking Cell | Arc Welding | ISUSU RG06 | 6 | 2020 |
15 | Front Seat Cross Member WF | Sopt Welding | Volkswagen AG MEB316(20001) | 4 | 2020 |
16 | Floor Pan WF and Grippers | Sopt Welding | AUDI/ PORSCHE PPE 41(19017 Phase 1) | 18 | 2020 |
17 | Wheel House WF and Grippers | Arc Welding | Ford BX755(19018) | 6 | 2020 |
18 | AB Ring WF and Grippers | Arc Welding | Ford BX755(19018) | 14 | 2020 |
19 | Dash Panel WF and Grippers | Sopt Welding | South Africa Ford T6(17028-1) | 10 | 2020 |
20 | Cowl WF and Grippers | Spot Welding | South Africa Ford T6(17028-3) | 6 | 2020 |
21 | Front End WF and Grippers | Spot and Arc Welding | South Africa Ford T6(17025) | 10 | 2020 |
22 | Rocker WF and Grippers | Spot Welding | South Africa Ford T6(19029) | 8 | 2020 |
23 | Floor Pan WF and Grippers | Sopt Welding | AUDI/ PORSCHE PPE 41(19017 Phase 2) | 63 | 2021 |
24 | Rear Bumper and Chassis WF | Arc Welding | Ford P703&J73 | 36 | 2020-2021 |
Major Welding Fixtures Project(2022) | |||||
Item | Description | Type | Project Name | Qty(Sets) | Year |
25 | Middle Channel Reinforcement WF | Sopt Welding | Vinfast VF36 | 8 | 2022 |
26 | Floor Pan WF and Grippers | Sopt Welding | AUDI/ PORSCHE PPE 41(19017 Phase 3&4) | 39 | 2022 |
27 | Floor Pan WF | Sopt Welding and Projection Welding | Ford P703 PHEV | 29 | 2022 |
28 | Floor Pan WF and Grippers | Sopt Welding | Porsche E4 Floor Pan(21050) | 16 | 2022 |
29 | Floor Tunnel WF | Laser marking | VW Floor Tunnel(21008 ) | 2 | 2022 |
30 | Seat ASSY WF and Tooling | Arc Welding | BYD Seat ASSY | 40 | 2022 |
31 | Floor Pan WF | Spot and Arc Welding | Ford Refurbishment | 24 | 2022 |
32 | CCB WF | Arc Welding | VW Cyclone CCB(21037) | 10 | 2022 |
33 | CCB WF | Arc Welding | VW MQB37(22022) | 16 | 2022 |
34 | A&B-Pillar WF | Spot Welding | Gestamp GS2203 | 8 | 2022 |
35 | Robot Cell Base | NA | VW Cyclone | 4 | 2022 |
Welding Fixture Manufacturing Center
We can build all kinds of different size welding fixture including large size as we have big CNC Machines. With a variety of mechanical equipment such as milling, grinding, wire cutting machines and drilling machines, we can effectively and accurately control the processing process.
25 sets of CNC with 2 shift running
1 Set of 3-Axis CNC 3000*2000*1500
1 Set of 3-Axis CNC 3000*2300*900
1 Set of 3-Axis CNC 4000*2400*900
1 Set of 3-Axis CNC 4000*2400*1000
1 Set of 3-Axis CNC 6000*3000*1200
4 Set of 3-Axis CNC 800*500*530
9 Set of 3-Axis CNC 900*600*600
5 Set of 3-Axis CNC 1100*800*500
1 Set of 3-Axis CNC 1300*700*650
1 Set of 3-Axis CNC 2500*1100*800
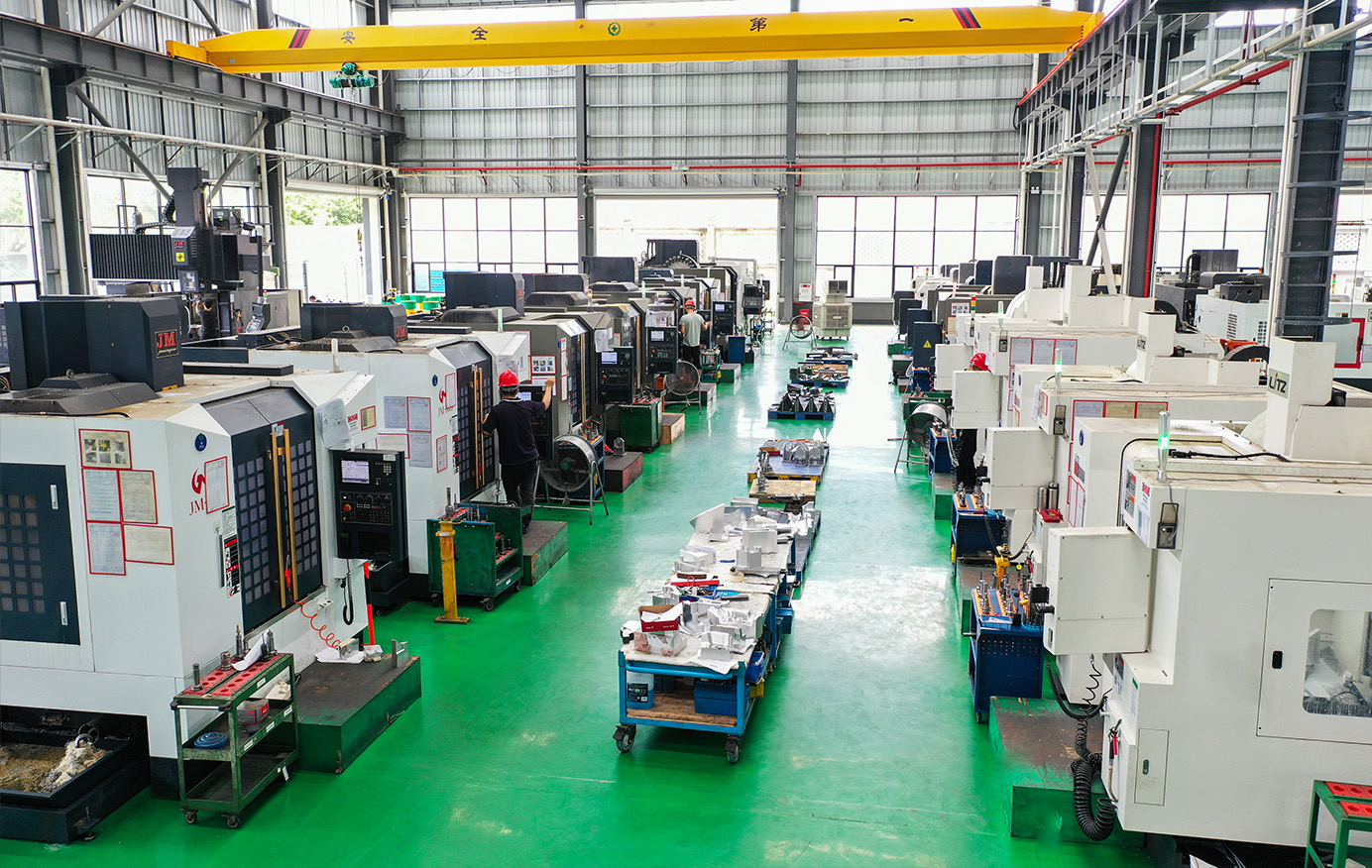
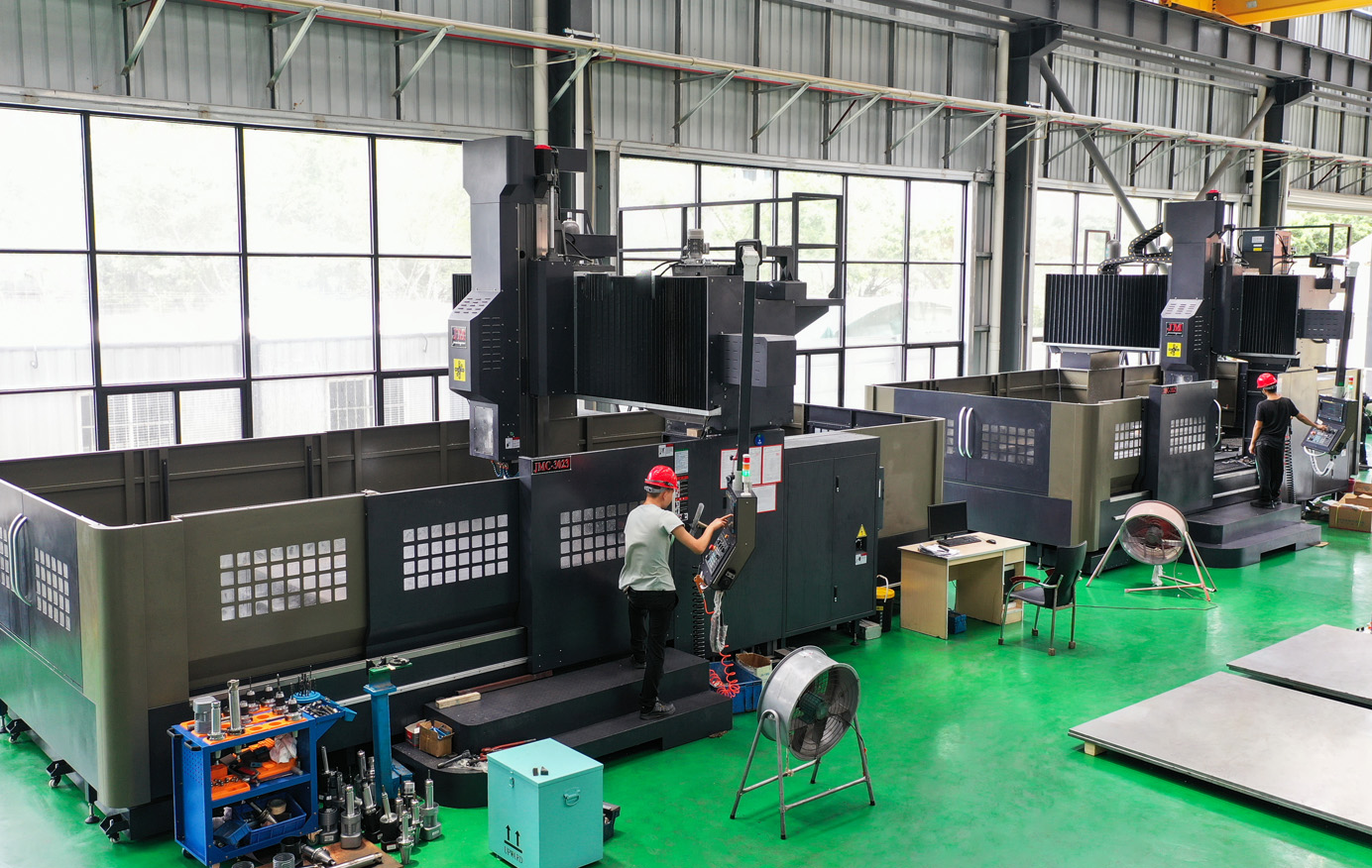
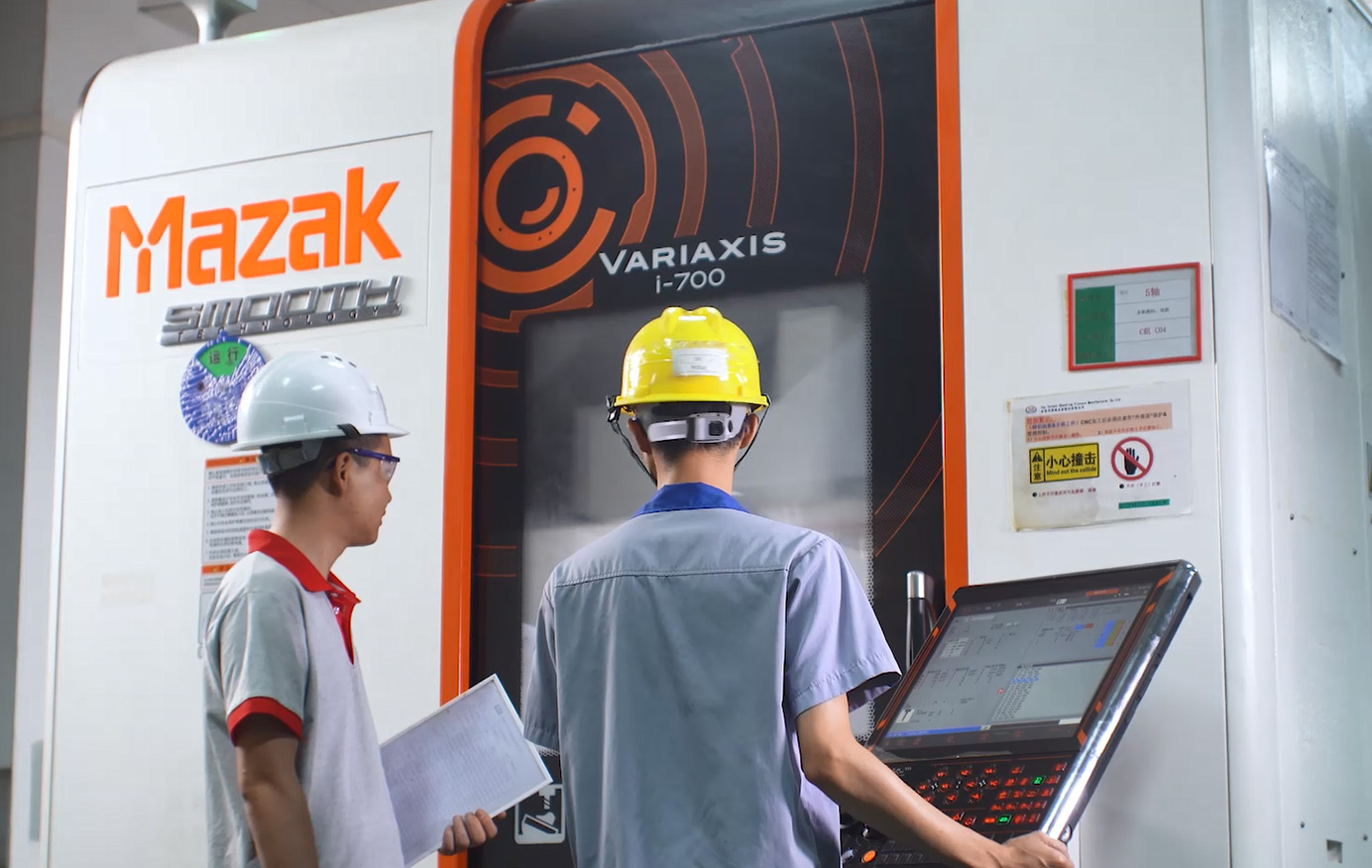
5 Axis CNC -Machine
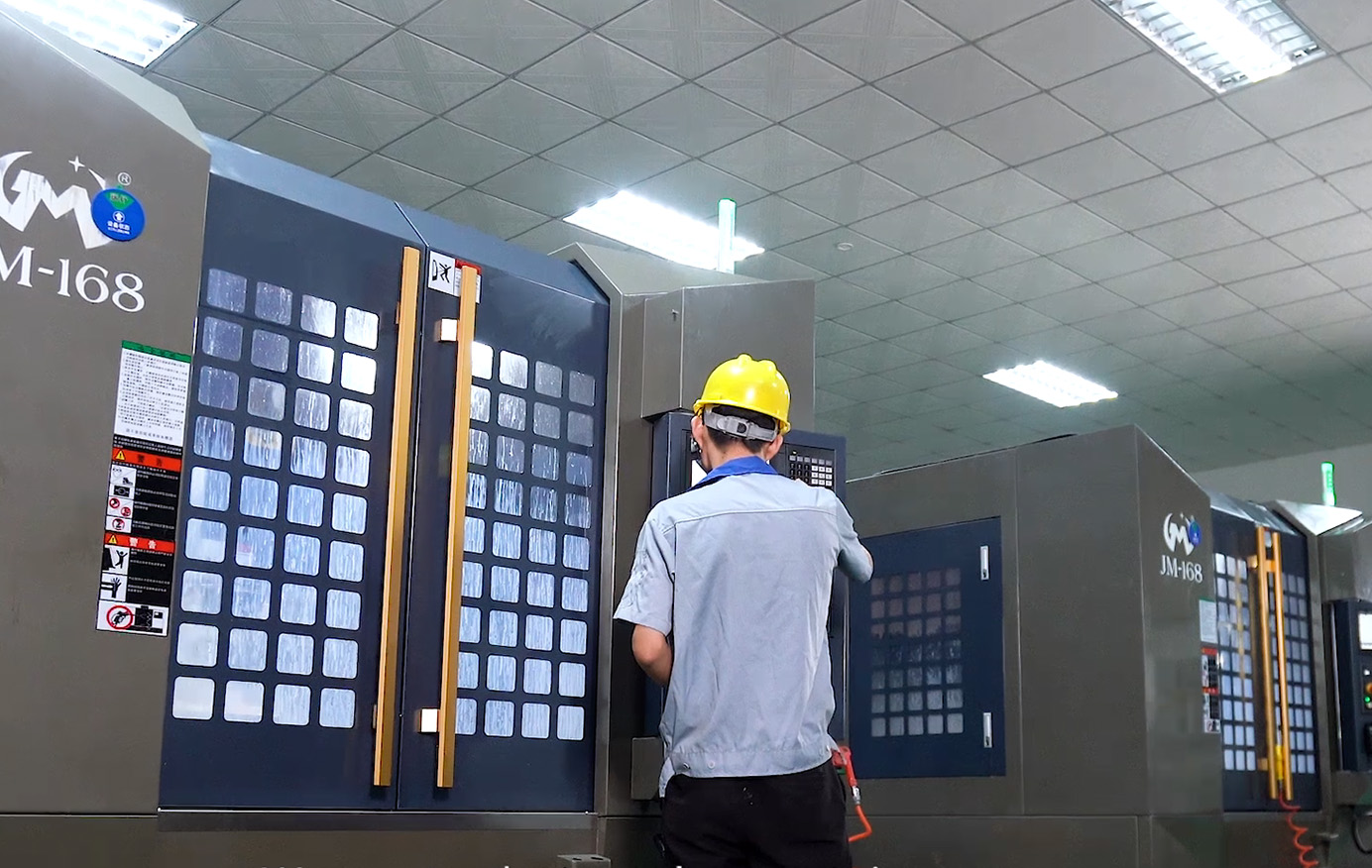
4 Axis CNC -Machine
Welding Fixture Assembly Center
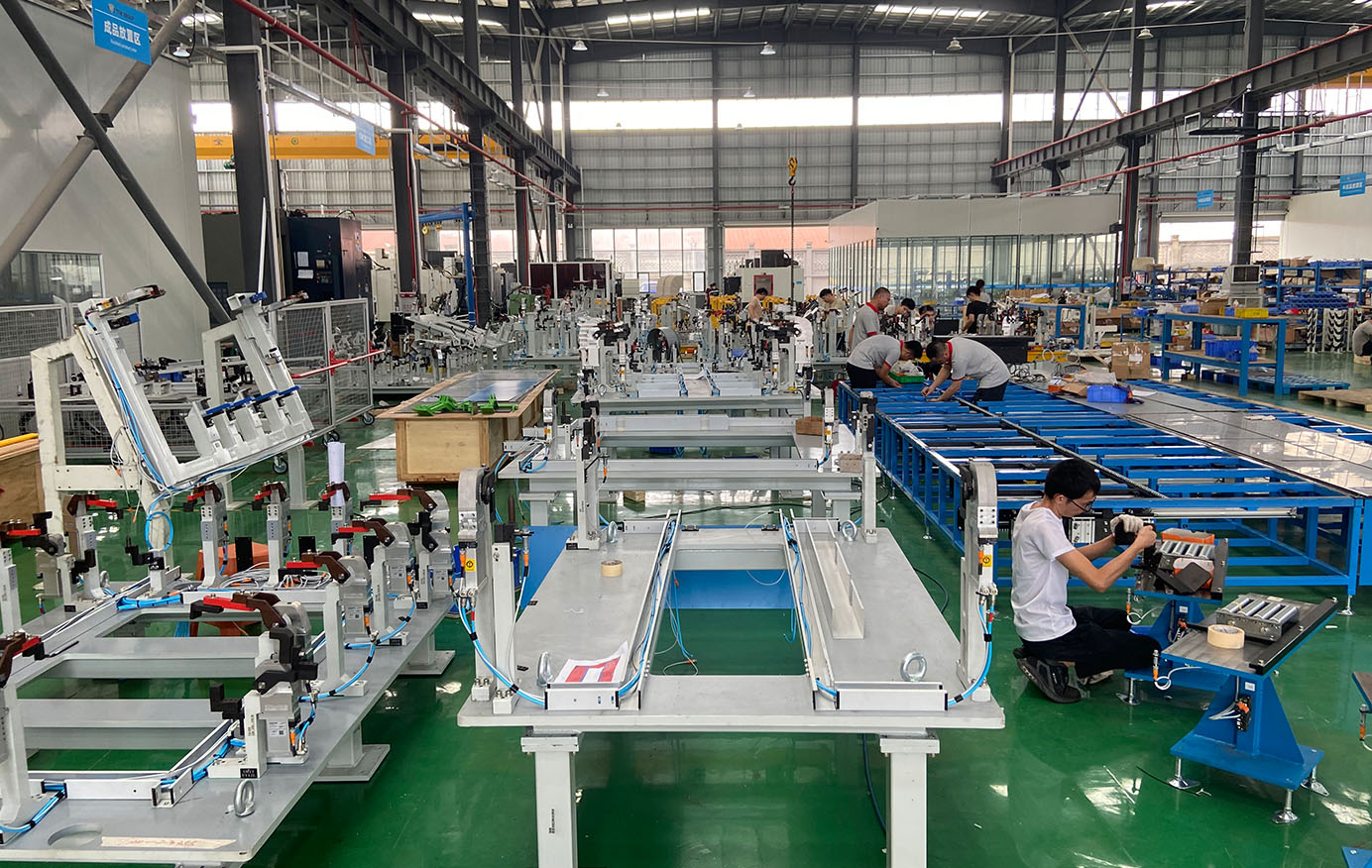

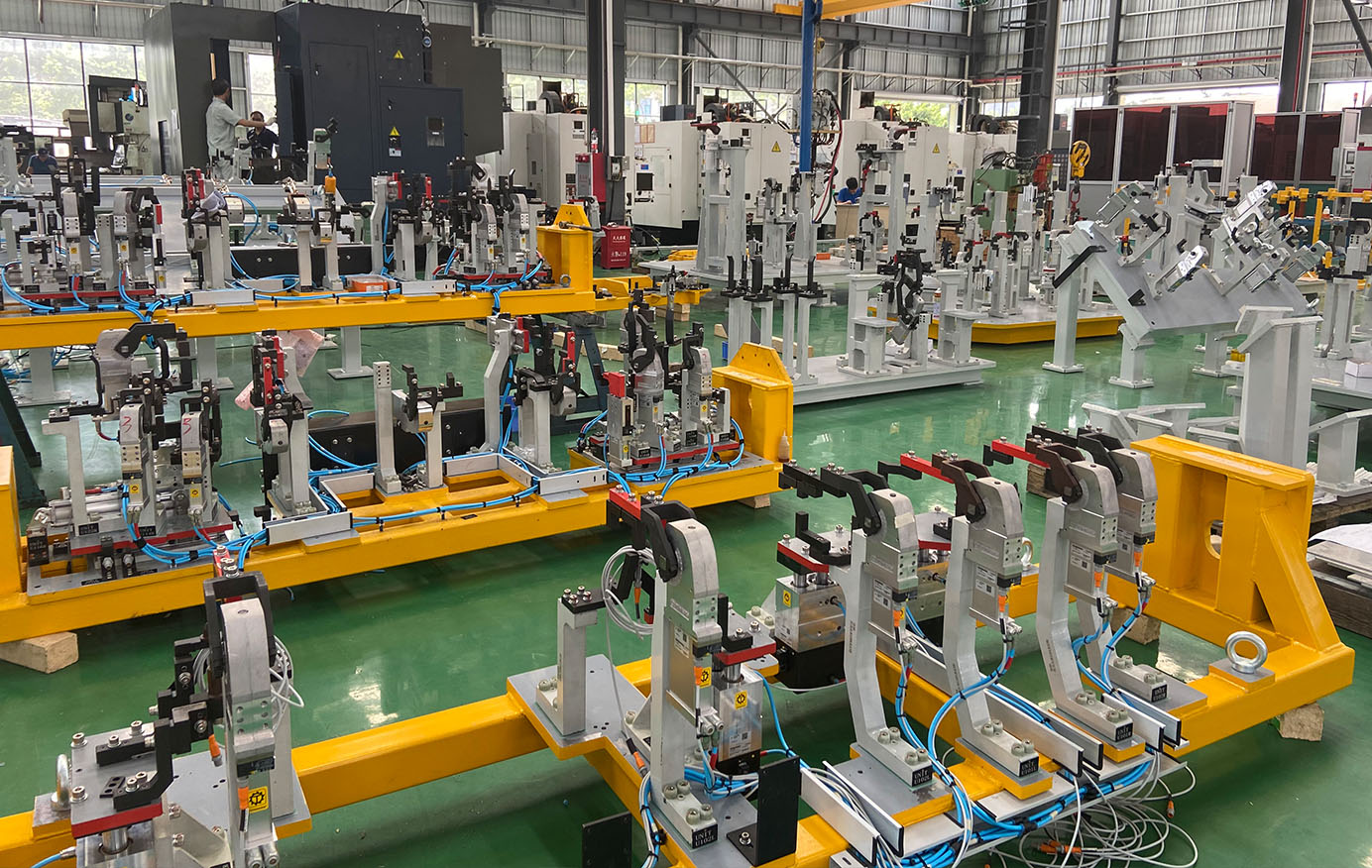
CMM Measurement Center For Welding Fixture
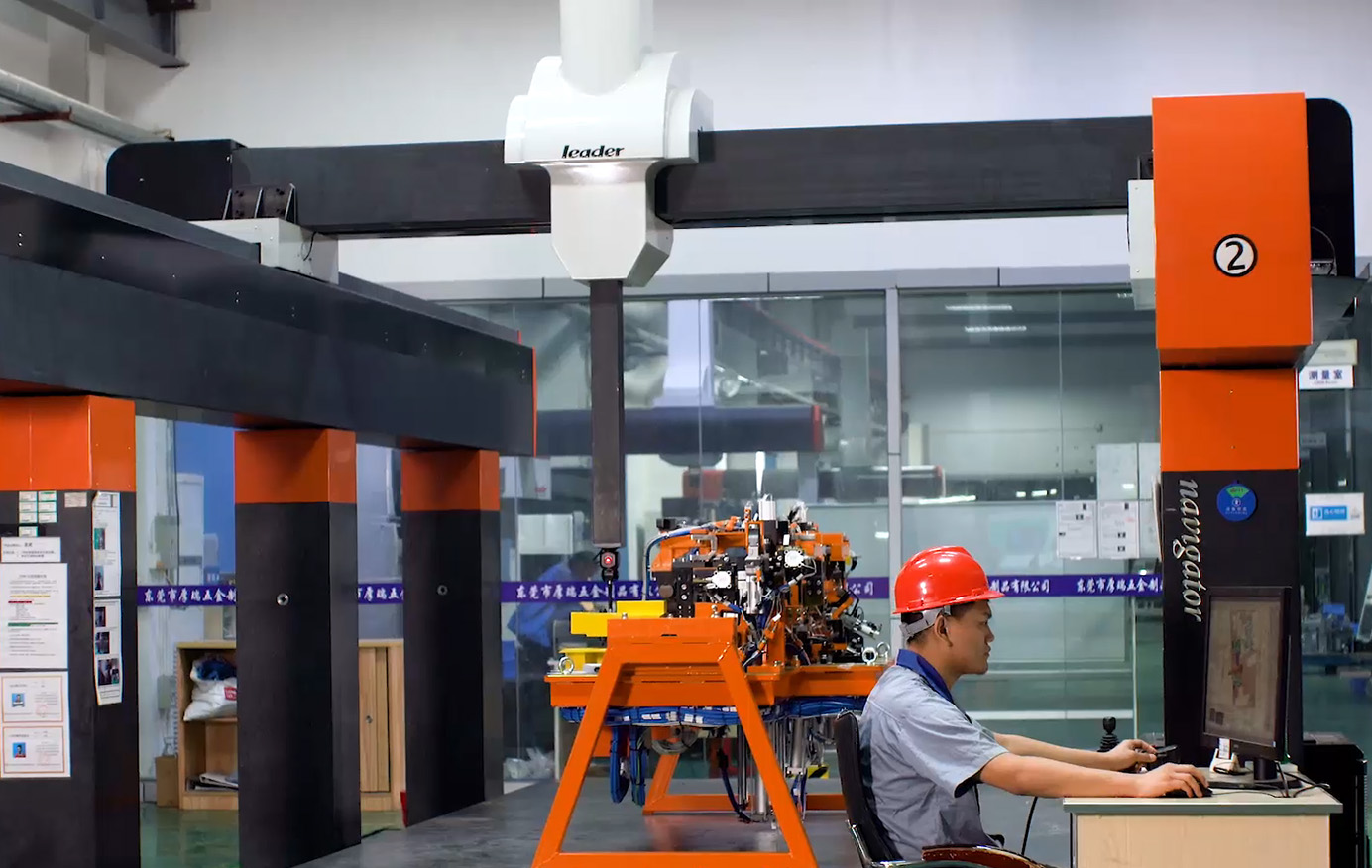
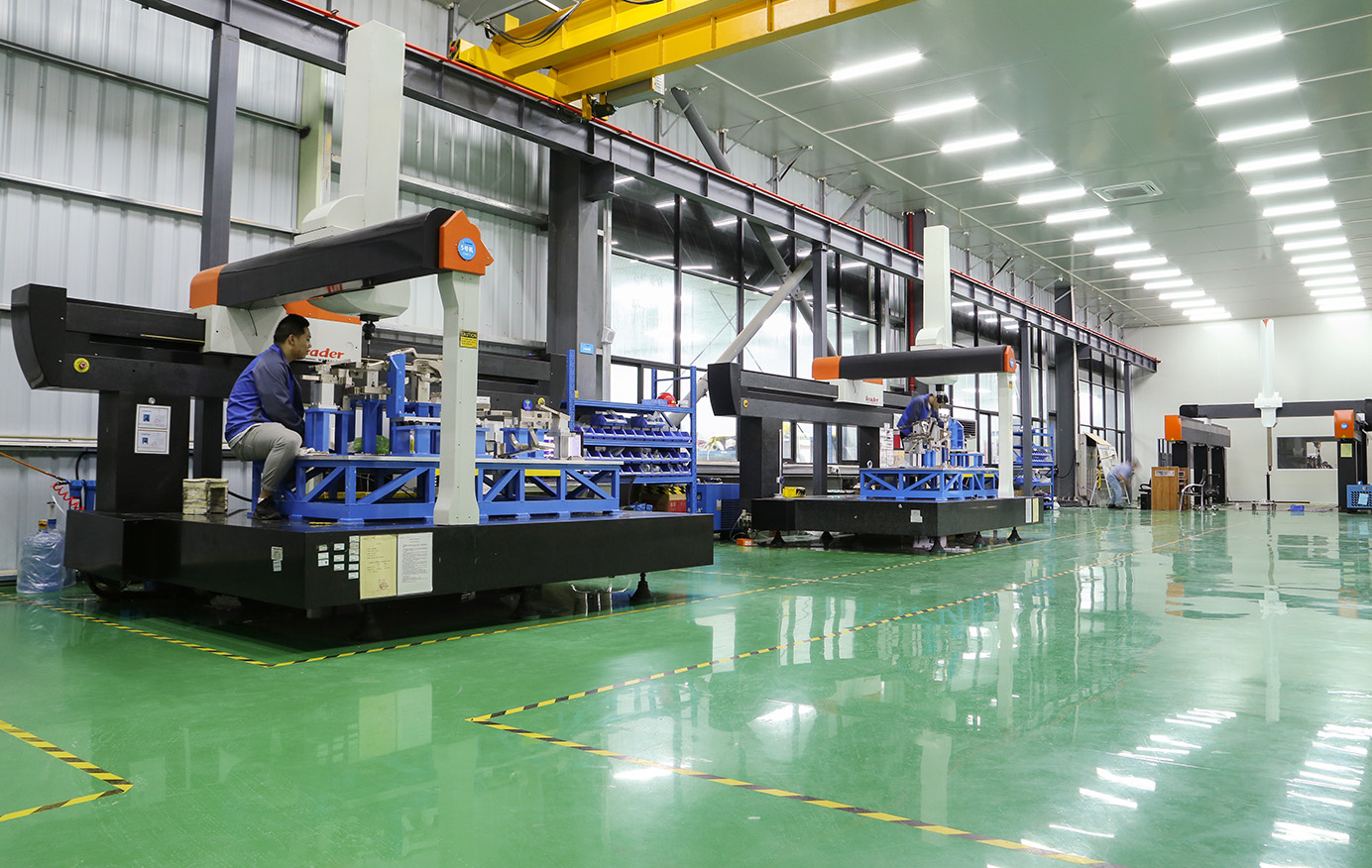
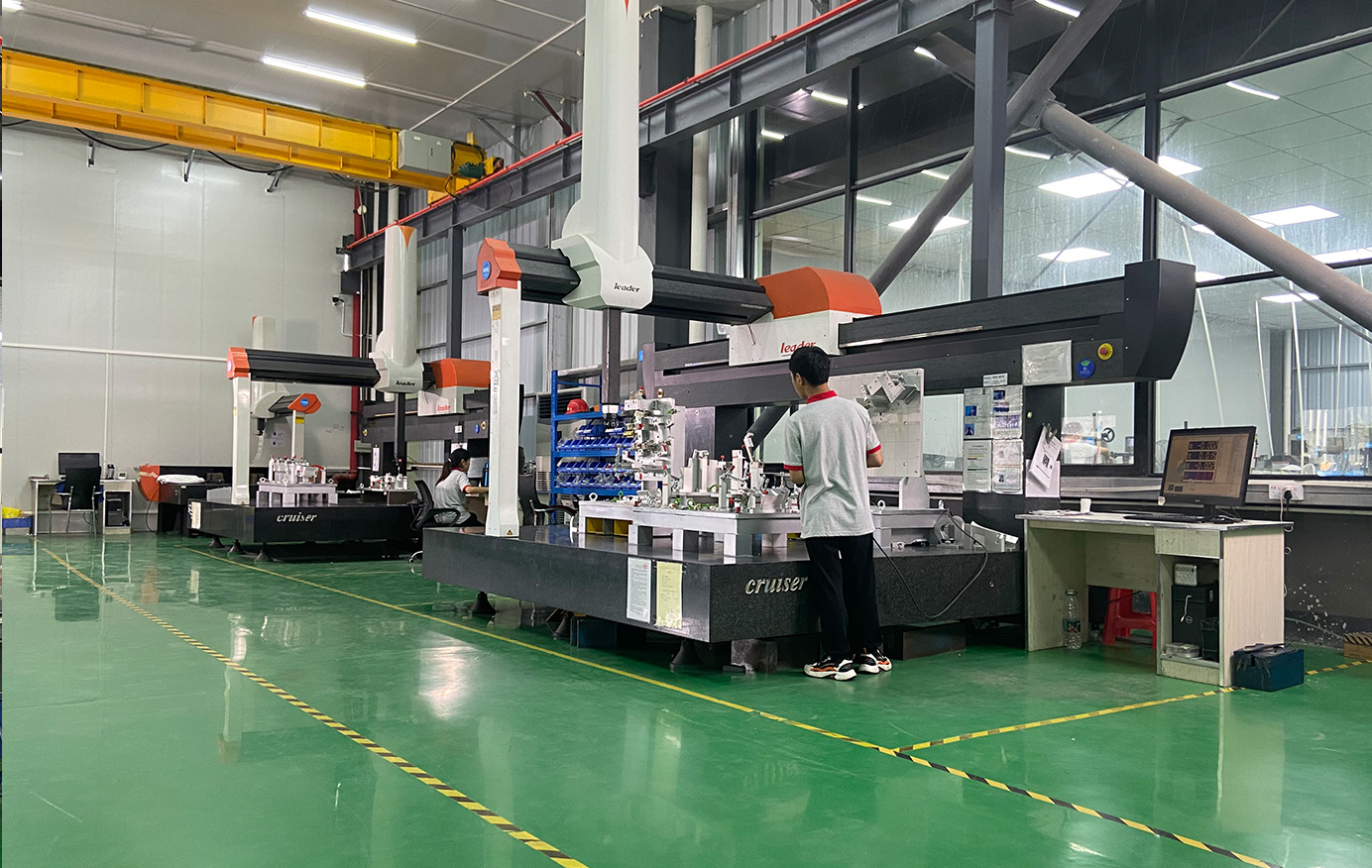
Our good trained personnel will take care every time in every program we have. We can do every requirement from the customer, to have the biggest satisfaction in the CMM as well.
3 Sets of CMM, 2 Shifts/Day(10hrs per shift Mon-Sat)
CMM, 3000*1500*1000 , Leader CMM, 1200*600*600 , Leader Blue-light Scanner
CMM, 500*500*400, Hexagon 2D Projector, Hardness Tester