2022 New Style Dies & Tools Ltd - OEM custom high precision progressive punching deep drawing mould casting and sheet metal mold stamping die tooling – TTM
2022 New Style Dies & Tools Ltd - OEM custom high precision progressive punching deep drawing mould casting and sheet metal mold stamping die tooling – TTM Detail:
Function
Progressive die, also known as continuous die, the die has two or more than two stations, can complete two or more than two stamping process in different stations.
Application Fields
Automotive industry for parts of car.
Automotive production line production capacity improve.
Product Details
Detailed Introduction
The basic requirements of the die design work are: the design of the die should ensure that the parts out of the drawing in line with the shape and size requirements, die structure is simple, firm installation, convenient maintenance, durable; Easy to operate, safe and reliable work; Easy to manufacture, low price.
The general steps of die design
First, collect the necessary information, analysis of the stamping process. Including: should have a complete view, technical requirements clear drawings or samples, to the shape of the parts, size, precision requirements and assembly relations have a comprehensive understanding; Understand the part stamping process card (usually provided by the stamping technician), so as to study its before and after. The relationship between the processes and the processing process requirements must be mutually guaranteed between the processes, and the number and type of die shall be determined according to the process plan specified in the process card; Master the production nature of the parts (trial production or batch or mass production) to determine the mold structure, is the use of simple mold or more complex high productivity mold; Understand the nature, size and supply method of the component material, such as sheet material or strip material, roll material or scrap material; Understand the press and related technical specifications, determine the unloading method and other auxiliary procedures of the mold according to the selected equipment:
Understand the technical force, equipment conditions and processing skills of mold manufacturing, to provide a basis for determining the structure of the mold. On the basis of the research and understanding of these data, if it is found that the stamping process is poor, it should be in the case of not affecting its performance, put forward to facilitate the modification of processing, so that product design, stamping process preparation, mold design and mold manufacturing between the better combination, to achieve a more perfect effect.
Second, determine the technical and economic parts are more reasonable stamping process scheme. According to the shape of the parts, dimensional accuracy, surface quality requirements for process analysis, determine the nature of the basic process, such as blanking, punching, bending and other basic processes (this simple process nature, generally can be directly from the requirements of the parts chart to determine >; According to process calculation to determine the number of processes, such as drawing times, etc.; According to the deformation characteristics of each process, size requirements to determine the sequence of process arrangement, if the first punching after bending or bending after punching; According to the production batch and conditions to determine the process combination, such as composite stamping process, continuous stamping process, etc.
Third, the choice of mold form. When the nature of the process, the sequence and the combination of the process is determined, that is, to determine the stamping process scheme, at this time should also determine the process of the mold structure form (mold form selection see the following description).
Fourth, the necessary process calculation. Mainly includes: calculation of blank size, in order to arrange the sample under the most economic principle and reasonable determination of the use of materials; Calculate the punching pressure (including punching force, bending force, tensile force, unloading force, pushing force, blank holder force, etc.) in order to determine the press; Calculate the pressure center of the die, so as not to affect the quality of the die by eccentric load; Calculate or estimate the main parts of the mold (concave die, punch fixed plate, pad, punch, etc.) dimensions, as well as the free height of the discharge rubber or spring; Determine the clearance of convex and concave die, calculate the size of convex and concave die working part; Determine whether the blank holder is used for the drawing die, the number of drawing and the middle. Process mold size distribution and semi-finished product size calculation.
Fifth, the overall design of the mold. On the basis of the above analysis and calculation, the overall mold design can be carried out. Generally, the structure is sketched first, and the closing height of the mold is preliminarily calculated, and the shape size of the mold is roughly determined. At this time, the structure of each component can be designed to determine the rough scheme. It should be noted that these steps are closely linked, integrated and complementary to each other to determine the best solution. In general, the overall design is carried out while considering the design of the component structure. The sequence is not absolute. Component structure design mainly includes the following contents:
① Working parts. Such as punch, concave die and convex and concave die and other structural forms are integral, combined or inlaid, and fixed form determination.
② Locate the parts. Such as the use of positioning plate, baffle pin (fixed or movable), etc., its form is many, can be selected or designed according to the specific situation. For progressive die, also consider whether to use the initial baffle pin, guide pin and distance punch (side edge).
③ Unloading and pushing device. Unloading is commonly used in two forms: rigid and flexible. The rigid printing material usually adopts the structure form of fixed unloading plate, and the flexible unloading material usually adopts the skin or spring as the elastic element (its spring or rubber needs to be designed and calculated).
④ Guide parts. Including whether a guide part is required and what form of guide part is used. If guide post · guide is used, the diameter and length of the guide post should be determined.
⑤ The selection of the mold frame, and its installation and fixation.
Sixth, choose the press. The selection of press is an important part of die design, and the type and specification of press must be determined during die design. The determination of press type mainly depends on the requirements of stamping process and the structure of die.
The Working Flow
1. Received the purchasing order -——-> 2. Design -——-> 3. Confirming the drawing/solutions -——-> 4. Prepare the materials -——-> 5. CNC -——-> 6. CMM -——-> 6. Assembling -——-> 7. CMM-> 8. Inspection -——-> 9. (3rd part inspection if need) -——-> 10. (internal/customer on site) -——-> 11. Packing(wooden box) -——-> 12. Delivery
Lead time & Packing
45 days after 3D design approved
5 days via express: FedEx by Air
Standard Export Wooden Case
Product detail pictures:

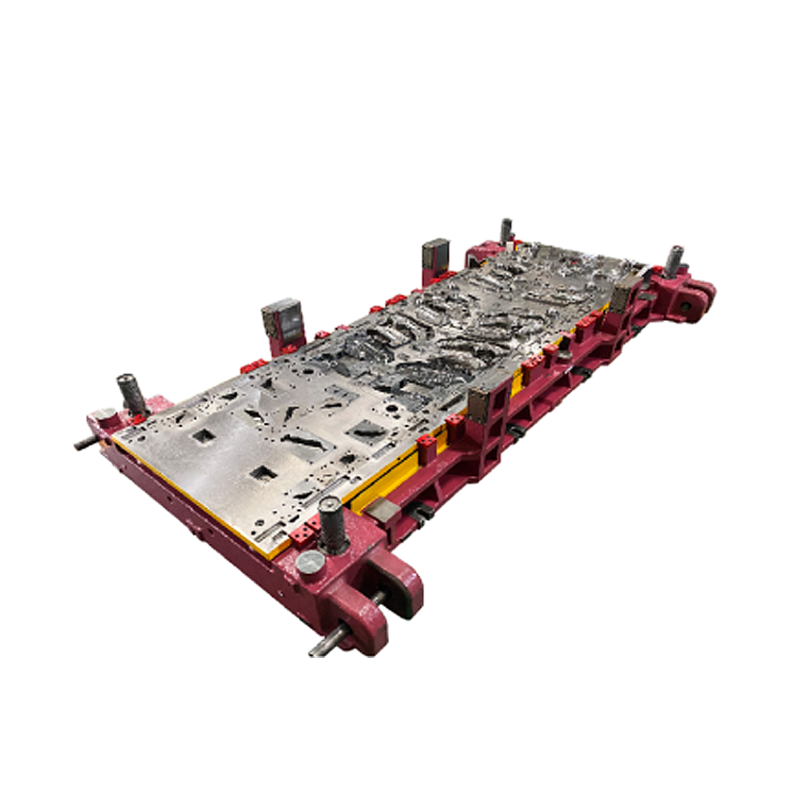






Related Product Guide:
The really abundant projects management experiences and 1 to just one provider model make the high importance of business enterprise communication and our easy understanding of your expectations for 2022 New Style Dies & Tools Ltd - OEM custom high precision progressive punching deep drawing mould casting and sheet metal mold stamping die tooling – TTM , The product will supply to all over the world, such as: New Delhi, Mombasa, Norwegian, Our company offers the full range from pre-sales to after-sales service, from product development to audit the use of maintenance, based on strong technical strength, superior product performance, reasonable prices and perfect service, we'll continue to develop, to deliver the high-quality items and services, and promote lasting cooperation with our customers, common development and create a better future.

Product variety is complete, good quality and inexpensive, the delivery is fast and transport is security, very good, we are happy to cooperate with a reputable company!
